A Shenzhen dental lab successfully created a full edentulous jaw implant prosthesis using digital restoration. The lab used the SHINING 3D DS300 Dental Scanner, exocad software, and received guidance from Spanish technician Waldo Zarco Nosti.
3D scanning the models and scan bodies
During the preparation stage, the dental technician used six scan bodies and screwed them onto analogs inside the plaster model. He proceeded to 3D scan them with the DS300. Then, to ensure that the scan bodies were correctly in place, he removed the artificial gingiva.
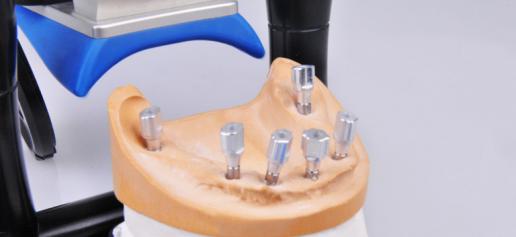
After completing this preparatory work, the technician scanned all the other necessary elements with the DS300 lab 3D scanner. He scanned the upper and lower occlusion models, the jaw model, the working model with artificial gingiva, and the working model with scan bodies.
For the upper and lower occlusion models, the technician used a special fixture. The markers on the fixture help the scanner identify the model’s spatial position of the model, facilitating the transfer of the positional relationship into dental CAD design software.
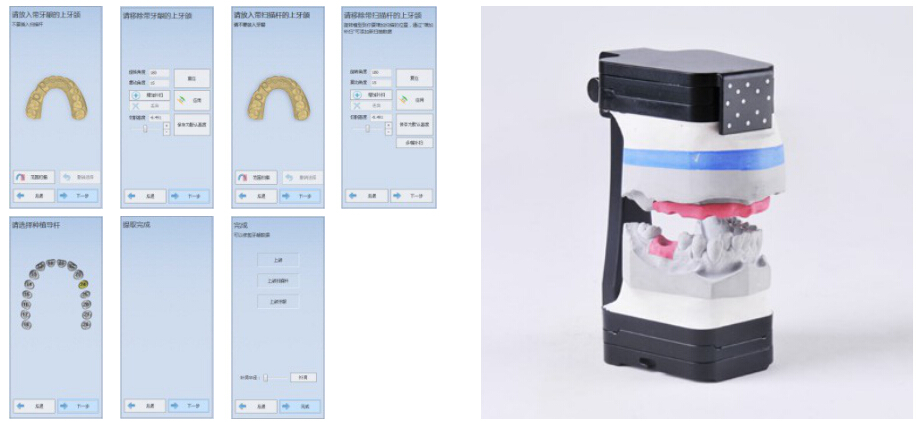
Preparing the full edentulous jaw implant restoration in exocad
After obtaining the 3D scanning data, Spanish technician Waldo Zarco Nosti designed the prosthesis with exocad.
Within exocad, Waldo selected the platform’s CAD data and aligned it with the scanned data to obtain the best match. This alignment step is critical, as it determines whether the upper structure can achieve a “passive fit”.
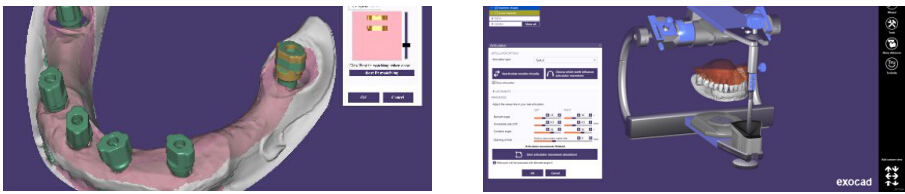
Thanks to the DS300’s bite relationship transfer tool, it was possible to transfer the spatial relationship between the jaw models and the dental articulator into the virtual articulator within exocad.
The position of the digital model inside the virtual articulator was consistent with the position of the plaster model inside the physical articulator. Therefore, the occlusal movement could be completely simulated within the software so as to eliminate intersections that might appear on the prosthesis during movement.
Based on the complete anatomic form of the previous step, the model is cut back into the basal framework. Mesial-distal retention grooves are prepared using a carving tool.
Producing the full jaw prosthesis
With the basal bridge design ready, a five-axis milling machine made the metal bridge.
Lastly, the technician used light-cured resin for the finish coating. He was then able to perform the aesthetic repair of red-white areas.